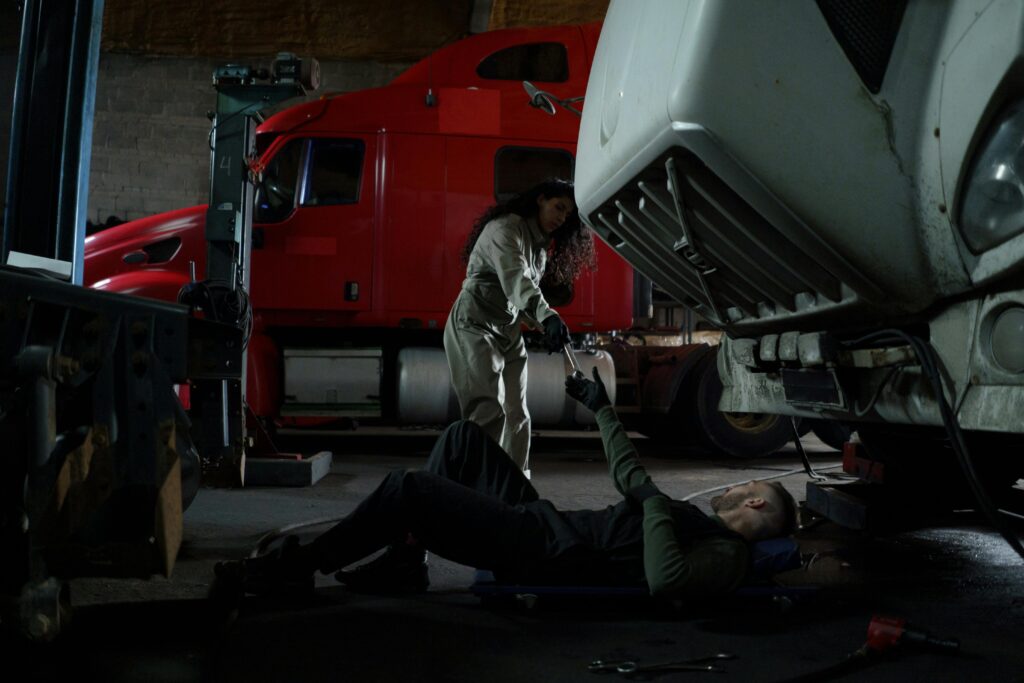
In the fast-paced world of transportation, minimizing downtime is a top priority for every fleet manager or truck driver. Why? Because the ticking clock in this industry represents more than just passing time. It symbolizes potential revenue slips and supply chain disruptions. Every second a truck spends off the road, even when it is to conduct necessary repairs, comes with a cost.
Recognizing the significance of swift and effective truck repairs, here are six comprehensive strategies we employ to help you get your trucks back on the road in no time.
- Proactive Maintenance Schedules
The first line of defense against unexpected breakdowns is a well-structured maintenance schedule. Kobo360 understand this, and to this end emphasize the importance of proactive maintenance, encouraging transporters to adhere to regular servicing intervals. We also provide transporters with access to a marketplace where they can purchase essential spare parts. This allows you to repair and address potential issues before they escalate, preventing costly repairs and keeping your trucks in optimal condition.
- Collaboration with Certified Service Providers
In the event of a breakdown, time becomes a critical factor. Hence, our dedicated customer service team are always on deck to facilitate collaboration with a network of certified service providers, ensuring that all transporters partnered with us have access to skilled technicians who can swiftly diagnose and repair issues. This collaborative approach minimizes the downtime associated with locating suitable repair services and expedites the return of trucks to the road.
- Predictive Analytics for Component Wear
Anticipating when components are likely to require replacement is a key strategy in reducing downtime and Kobo360 fleet management software utilizes predictive analytics to assess the wear and tear of critical truck components. By replacing parts before they fail, transporters can avoid unexpected breakdowns and the subsequent downtime associated with extensive repairs.
Also, fleet management software tracks the entire maintenance history of a vehicle, and can be used to determine the life cycle of a vehicle. Consequently, where a truck needs to be replaced, instead of repaired, this information can be used to make the decision.
- Remote Assistance and Telematics
In situations where immediate physical assistance is challenging, Kobo360 employs remote assistance and telematics solutions with skilled experts. Transporters can connect with technicians remotely, providing them with real-time insights into the truck’s condition. This virtual collaboration allows for quicker diagnosis and troubleshooting, reducing your truck/fleet overall downtime.
- Comprehensive Driver Training Programs
Well-trained drivers are an asset to any fleet and play a significant role in preventing accidents and mechanical failures. Hence, Kobo360 places a strong emphasis on driver training programs and occasionally carry out such trainings to ensure that your team is equipped to handle minor issues on the road, reducing the need for external assistance and minimizing downtime.
Conclusion
To sum up, often downtime is inevitable. However, you can maximize your truck uptime with these strategic solutions and a partner that is committed to ensuring that your vehicles spend more time on the road making you money and less time in the repair shop. What are you waiting for? Send us an email or fill this form so we can the worrying off your shoulders.
Leave a Reply